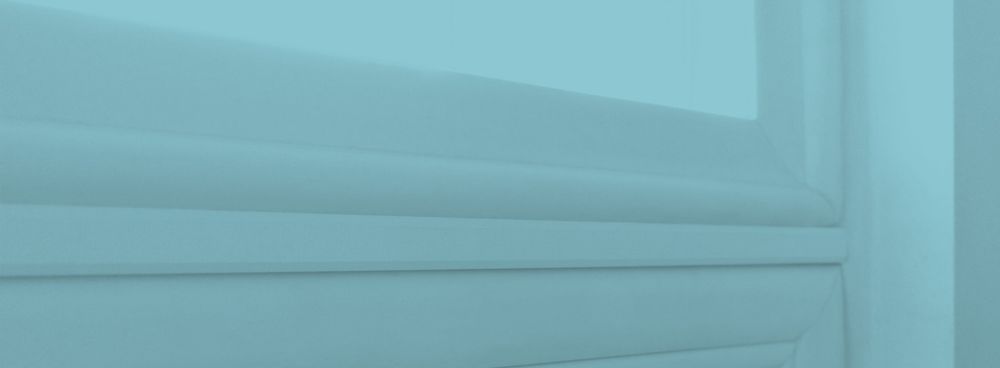
Ways to Save with Energy Efficiency in Your Home
Indow Innovations Brought the Missing Piece to Window Inserts
You might have noticed that the back corners of our Indow window inserts have a piece missing. It’s not really missing, it’s designed that way. The cut out piece prevents the corner from buckling and creating gaps between the tubing and window frame. It’s how we get the most insulated windows.
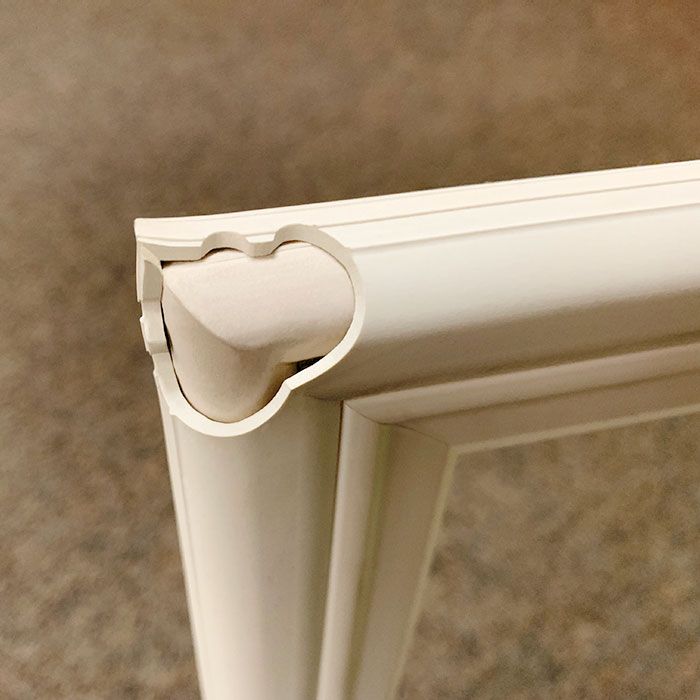
When the window inserts are pressed into place, there is compression all along the tubing. The corner piece of the frame is compressed from two different directions at once. To absorb that compression, the cutout allows the corner piece to rotate back into the window frame. The “corner brace” as we call it, gives the corner of the tube the rigidity it needs to spring back and allows the corners to be snug and tight without buckling.
The material you see exposed—the corner brace—is a smaller foam silicone tube that sits inside the larger silicone tube edging the acrylic panel. Our window inserts didn’t start out that way.
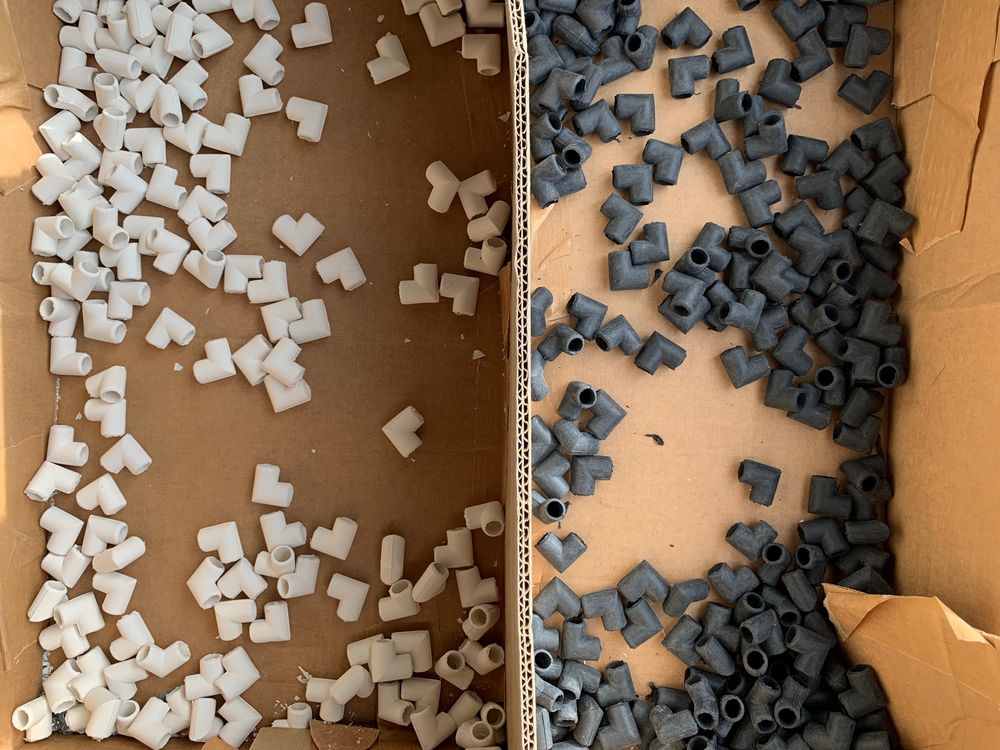
We knew some part of our solid tubing surrounding the window inserts had to be removed in order for our compression system to work. We used to hand punch ¾” round dots from sheets of open cell foam and individually glue them into the corners. Someone would be sitting there with a round punch and a hammer and just whack, whack, whack… But those pieces would become discolored and lose their springiness over time.
Now we have them molded out of silicone, saving us production time and giving us a more functional and durable solution. We simply cut out part of the really strong silicone tubing, pop the reinforcing corner brace inside, which allows a graceful collapse, but keeps it strong enough to fill in the corner without any gaps.
It’s a simple and elegant solution to ensure our window inserts have the best compression and create the most insulated windows. Indow window inserts are always improving thanks to our innovative and creative team.